ANWENDUNGSHINWEIS
Warum das Kabel-Prüfgerät kalibrieren?
PDF herunterladen
Auf dieser Seite
Einleitung
Sie nehmen Ihre Kabelprüfgeräte ernst. Sie kaufen Spitzenmarken und Sie erwarten, dass sie genau sind. Sie wissen, dass manche Benutzer ihre Testgeräte zur Kalibrierung zu einem Labor schicken und Sie wundern sich warum. Schließlich sind sie alle elektronisch - es gibt keine mechnanischen Teile, die aus der Kalibrierung driften können. Was machen diese Kalibrierungstypen, die Batterie austauschen?
Das sind gültige Bedenken, besonders da Sie Ihr Testgerät nicht benutzen können, während es zur Kalibrierung ausgesendet ist. Aber lassen Sie uns gewisse andere gültige Bedenken aufwerfen. Zum Beispiel: Was wäre, wenn ein Ereignis Ihr Testgerät weniger präzise oder möglicherweise sogar unsicher machen würde? Was wäre, wenn Sie mit engen Toleranzen arbeiten und genaue Messungen wichtig für den ordnungsgemäßen Betrieb von teuren Prozessen oder von Sicherheitssystemen sind? Was wäre, wenn Sie NEXT- oder Dämpfungsverlusttrends über Ihre Projekte messen und zwei Testgeräte, die für die gleiche Messung benutzt werden, deutlich voneinander abweichen?
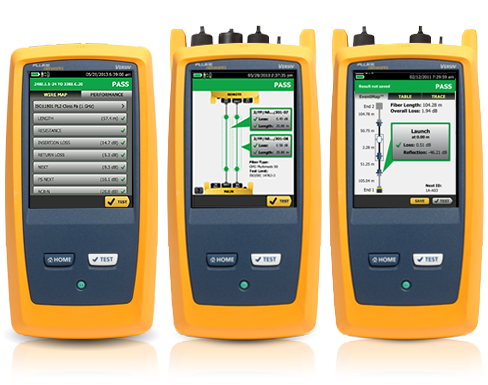
Warum das Kabel-Prüfgerät kalibrieren?
Feld-Zertifikation von strukturierten Datakom-Kabelinstallationen ist ein Spiel mit hohem Einsatz. Die Bezahlung für einen Auftrag hängt normalerweise von einer erfolgreichen Zertifikation aller Verbindungen ab, die häufig tausendfach vorhanden sind. Ein fehlerhaftes Prüfgerät kann auf verschiedene Arten zu Chaos führen. Nehmen Sie zum Beispiel an, dass das Prüfgerät fehlerhafte Verbindungen fälschlich als ordnungsgemäß anzeigt. In diesem Fall könnten zukünftige Benutzer des Systems Netzwerkprobleme erleben, die auf die Kabelanlage zurückführbar sind. Diese Probleme könnten zu rechtlichen Schritten gegen den Installateur führen, der auch für die Überarbeitung und Reparatur verantwortlich sein würde. Andererseits nehmen Sie an, dass das Prüfgerät gute Verbindungen als fehlerhaft bezeichnet. Dann verschwendet der Installateur Zeit und Geld mit Reparaturen und Nacharbeiten.
Das Fluke Networks Designteam konzentriert sich auf die Schaffung von robusten Prüfgeräten, deren Auslegung Genauigkeit und Zuverlässigkeit garantiert. Unser Produktionsteam bemüht sich, die Möglichkeit, ein defektes Instrument zu versenden, auf Null zu senken. Sobald jedoch ein Instrument im Einsatz ist, werden verschiedene unvermeidbare Faktoren aktiv, die die Leistung beeinflussen können.
Ein derartiger Faktor ist einfach der Ablauf von Zeit und die damit verbundenen Umweltbelastungen. Die Komponenten unserer Messsysteme sind in hohem Grade stabil und sind Geräte wie Widerstände, Kondensatoren und integrierte Schaltungen. Jedoch weisen diese Komponenten im Laufe der Zeit unvermeidlich geringfügige Veränderungen auf, in großem Maße aufgrund von normalen Änderungen in Temperatur und Luftfeuchtigkeit, die sowohl im Betrieb als auch beim Lagerung und Transport auftreten. Ein Instrument könnte die Nacht bei Temperaturen unter dem Gefrierpunkt in einem Kofferraum verbringen, gefolgt vom schnellen Aufwärmen in einer normalen Büroumgebung für die tägliche Arbeit. Selbst in einer kontrollierten Umgebung wärmen sich die Schaltkreisbaugruppen auf und kühlen sich ab aufgrund der Leistungsaufnahme des Messinstruments beim Ein- und Ausschalten im Verlauf des Tages. Ein weiterer, heimtückischerer Faktor könnte ein Defekt sein, der durch ein extremes Umgebungsereignis verursacht wurde. Nehmen Sie an, dass ein Instrument von einer hohen Leiter auf einen Betonboden fällt. Sehr wahrscheinlich übersteht das das Instrument, da wir Stoßfestigkeit einplanen und rigorose Qualifikationstests durchführen. Aber eine Komponente könnte sich dennoch lösen oder anderweitig beschädigt werden. Diese Komponente verursacht möglicherweise feine Verminderungen in der Genauigkeit, was zu falschen negativen oder positiven Ergebnissen führt. Oder nehmen Sie an, dass ein Instrument mit einem Material verunreinigt wird, das die reine Oberfläche einer Leiterplatte kompromittiert. Dies könnte zu einem Leckstrom führen und die Präzision von Widerstandsmessungen beeinträchtigen. Offenbar können uns wir die erwarteten und unerwarteten Faktoren vorstellen, die im Laufe der Zeit das Vertrauen in die Genauigkeit mindern.
Was ist Kalibrierung?
Alle diese Ungewissheiten können durch routinemäßige Kalibrierung des Instruments gemindert werden. Das hat mehrere Vorteile. Der erste Schritt in der Kalibrierung ist im Wesentlichen ein Messungsbewertungs- und -korrekturprozess, während dessen das Instrument an eine umfassende Reihe von Bezugskalibrierungsstandards angeschlossen wird. Das Instrument misst jeden Standard und speichert interne Korrekturdaten, damit folgende Messungen des Standards genau zentriert werden. Ein sehr nützlicher Nebeneffekt dieses Prozesses ist, dass gleichzeitig ein umfassender Selbsttest durchgeführt wird. Für jedes Artefakt werden die internen Kalibrierungsdaten des Instruments mit einer Pass/Fail-Vorlage verglichen. Fail zeigt einen fehlerhaften Stromkreis an. Diese Vorlagen wurden mittels strenger statistischer Analysen einer großen Population von Instrumenten ermittelt und dienen als sehr empfindlicher Test des Zustands des Instruments.
Der zweite Schritt beinhaltet einen Satz Überprüfungs-Artefakte. Diese Artefakte verhalten sich wie eine Kabelverbindung aus der Sicht des Instruments. Zum Beispiel ergibt das Einfügungsverlust-Artefakt eine Messung, die einer 100 Meter langen Kabelverbindung ähnlich ist. Die Artefakte werden als Übergangsstandards verwendet. Jedes wurde mit einem Laborsystem gemessen, das hochgenaue und NIST-nachführbare Werkbankgeräte einsetzt. Die resultierenden Daten werden archiviert und mit dem Testergebnis des Instruments verglichen. Der Unterschied ist die beobachtete Messgenauigkeit, die mit einer auf den Ungewissheitsspezifikationen des Instruments basierenden berechneten Durchlauf-/Ausfallgrenze verglichen wird.
Um zusammenzufassen: Der Prozess zentriert die Messungen des Instruments, führt einen sehr empfindlichen Selbsttest durch und überprüft die Genauigkeit gegen NIST-nachführbare Übergangsstandards. Der Eigner erhält sein Instrument in höchster Einsatzbereitschaft.
Kalibrierungshäufigkeit
Die Frage ist nicht, ob man kalibrieren sollte – wir können sehen, dass das klar ist. Die Frage ist, wann man kalibrieren soll. Wir können nicht mit Sicherheit den Genauigkeitsdrift jedes einzelnen Instruments voraussagen. Jedoch mit einer jahrzehntelangen Produktionsgeschichte und mit Zehntausenden Instrumenten weltweit im Einsatz haben wir eine feste empirische Basis zur Untermauerung unserer Empfehlungen bezüglich der Häufigkeit der Kalibrierung. Als allgemeine Regel empfehlen wir die Kalibrierung mindestens auf jährlicher Basis, als angemessene Balance zwischen Kosten/Stillstandzeit und dem Bewahren eines hohen Betriebsvertrauens.
Andere Umstände können zusätzliche außerplanmäßige Kalibrierungen erforderlich machen. Zum Beispiel sollte eine Kalibrierung vor dem Inangriffnehmen eines sehr großen Projekts in Betracht gezogen werden. Andererseits sorgt eine erfolgreiche Kalibrierung direkt nach einem Projekt für das höchste Vertrauen in die Genauigkeit der Ergebnisse für diesen Auftrag. Oder wenn ein möglicherweise schädliches Ereignis aufgetreten ist, wie ein schwerer Fall oder ein extremer Temperaturzyklus, sollte eine Kalibrierung in Betracht gezogen werden.
Während dieser Artikel sich auf die Kalibrierung von Testgeräten konzentriert, gilt die gleiche Argumentation für Ihre Module.
Bei der Kalibrierung geht es nicht um die „Feineinstellung“ Ihres Prüfgeräts. Statt dessen wird damit sichergestellt, dass man die Instrumente sicher und zuverlässig benutzen kann, um die genauen Testergebnisse zu erhalten, die Sie benötigen. Es ist eine Form der Qualitätssicherung. Sie sind sich des Werts bewusst, den das Testen von Kabeln hat, ansonsten hätten Sie wohl keine Testinstrumente. So wie Kabel getestet werden müssen, so müssen Ihre Prüfgeräte überprüft werden.
Erhalten Sie eine jährliche Kalibrierung kostenlos mit Gold Support
Gold Support beinhaltet eine Kalibrierung und Betriebsaktualisierung pro Jahr ohne zusätzliche Kosten. Ihre Kabelanalysegeräte und Glasfasermodule werden genau nach Werksspezifikationen (Kalibrierungszertifikat wird bereitgestellt - rückführbare Kalibrierung mit Daten ist gegen eine zusätzliche Gebühr verfügbar) mit den unternehmenseigenen Testverfahren von Fluke Networks präzise kalibriert und bei Bedarf angepasst bzw. mit Original-Ersatzteilen repariert. Zudem werden Software- und Firmware-Updates auf das Gerät gespielt. Das gesamte Zubehör wird getestet und gereinigt, und fehlerhafte Teile werden ersetzt. Abschließend wird eine Überprüfung der Leistungsfähigkeit durchgeführt. Die typische Bearbeitungszeit für die Kalibrierung ist 5 Werktage, aber Gold Mitglieds-Leihgeräte sind für BF-Kalibrierung verfügbar (in den meisten Regionen). Learn more about Gold Support at www.flukenetworks.com/goldsupport, contact your local representative or Gold Sales 888-283-5853.
Auch Nicht-Gold-Mitglieder können für Kalibrierungen oder Reparaturen hervorragenden Service in jedem autorisierten Fluke Networks Service-Center erhalten. Simply find the Service Center closest to you and they will help you with your Fluke Networks repair and calibration needs or contact us at 1-888-993-5853.